
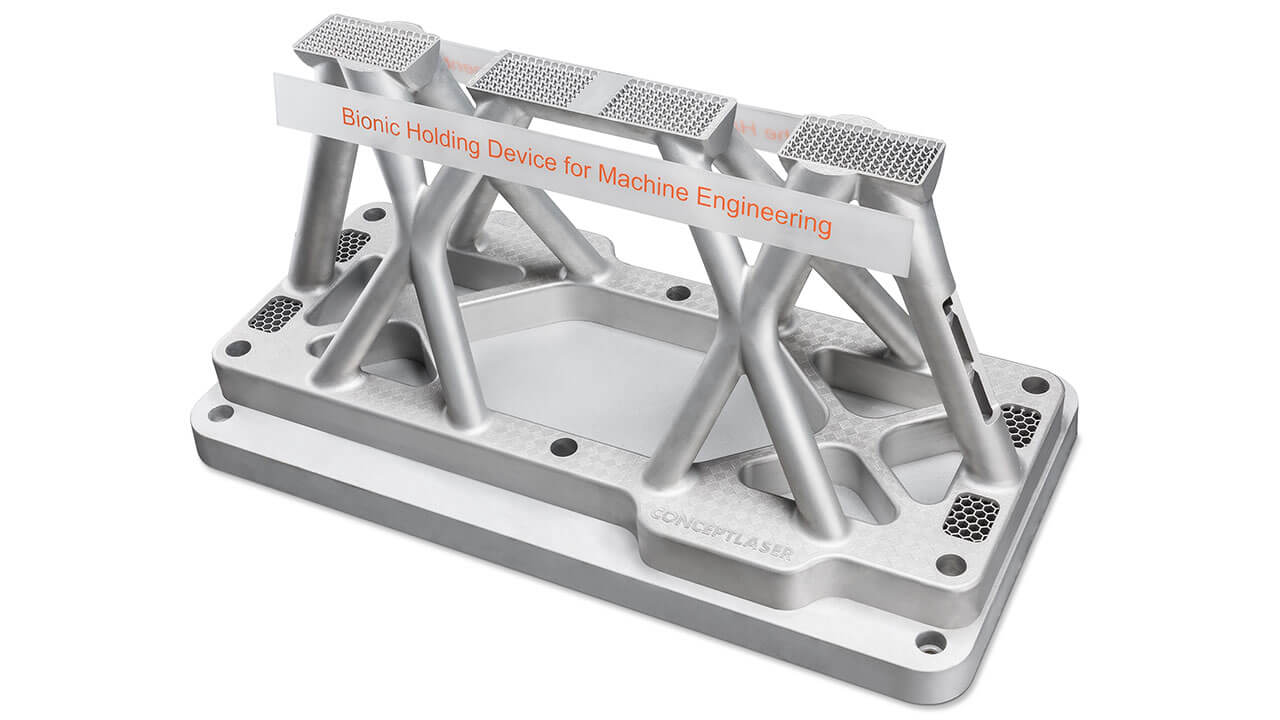
Metaal toevoegingsvervaardiging het ontwikkel tot 'n vervaardigingstegniek wat in verskeie bedrywe gebruik word. Finally, a solution for combining LPBF parts with conventional aluminium alloys is presented. This technology is used to produce weld seams that are then tested for their mechanical properties. By using laser welding in a vacuum, which is a newly developed and highly efficient laser welding process, the quality of the weld seams, especially in terms of porosity, can be improved. While it has been proven for different materials that conventional welding processes can be applied to LPBF manufactured parts, the resulting weld seam quality for AlSi10Mg is still insufficient. One solution to overcome this size limitation is to weld additive manufactured parts. But one of its major limitations is the size of the build chamber, which is limited to around 800 x 400 x 500 mm for the largest machine that is currently available. Especially in highly complex applications with small batches, such as aerospace or tooling, laser powder bed fusion (LPBF) has become established. Metal additive manufacturing has evolved to a manufacturing process used in different industries. VDepartment of Mechanical Engineering and Mechatronics, Aachen University of Applied sciences, Germany. IVDepartment of Chemical, Metallurgical and Materials Engineering, Faculty of Engineering and the Built Environment, Tshwane University of Technology, Pretoria, South Africa. IIDepartment of Mechanical Engineering and Mechatronics, Aachen University of applied sciences, Germany. IIwF GmbH - Institute for toolless fabrication, Germany. A Solukon powder removal system and a new Ipsen vacuum heat-treat furnace will also be added to Protolabs’ facilities to supplement its additive manufacturing equipment in the production of AS9100 components.Welding of additive manufactured ALSi10mg: using laser welding in a vacuum for high quality weld seams - a new approach to welding LPBF manufactured ALSi10mgĪ. In addition to the X Line 2000R, Protolabs has also acquired four more GE Additive Concept Laser M2 systems, bringing its total of Direct Metal Laser Sintering/ Melting machines to more than 30. “Through our partnership with GE Additive, we are responding by scaling up use of its cutting-edge equipment to further our customers’ metal production needs.” “Our customers, especially in the aerospace industry, have told us they need the ability to create larger parts with complex geometries,” commented Vicki Holt, President and CEO at Protolabs. Protolabs will use the system to produce components in Inconel 718 to ‘better serve its rapidly expanding number of aerospace customers.’ GE Additive’s Concept Laser X Line 2000R platform boasts a build volume of 800 x 400 x 500 mm, with two build modules allowing a build to be prepared while another takes place, and dual 1000W lasers. By integrating the X Line 2000R system this summer, Protolabs is set to enable its client base to harness additive manufacturing to produce large metal components. The service provider serves a host of vertical markets with its polymer and metal 3D printing equipment, boasting a range of processes including stereolithography, PolyJet, polymer powder bed fusion and Direct Metal Laser Sintering technologies.
#Concept laser xline install
Protolabs is to install the GE Additive Concept Laser X Line 2000R machine later this year as it expands its metal additive manufacturing capacity.
